
The enclosure and the liquid electrolyte work as the cathode in the wet tantalum capacitor. Wet tantalum capacitors use a liquid electrolyte to submerge the tantalum part and an enclosure covers wet tantalum capacitors. The last step is to add a cathode outside the dielectric. Each capacitor should have a safety margin oxide layer thickness to make sure reliable functionality. The dielectric thickness is directly related to the voltage proof of capacitors. In other words, tantalum capacitors have a higher capacitance value/ volume compared with other capacitors such as Aluminum capacitors.Īfter sintering, a dielectric is formed outside the tantalum particle surfaces by transforming the outside tantalum layer into Ta2O5.
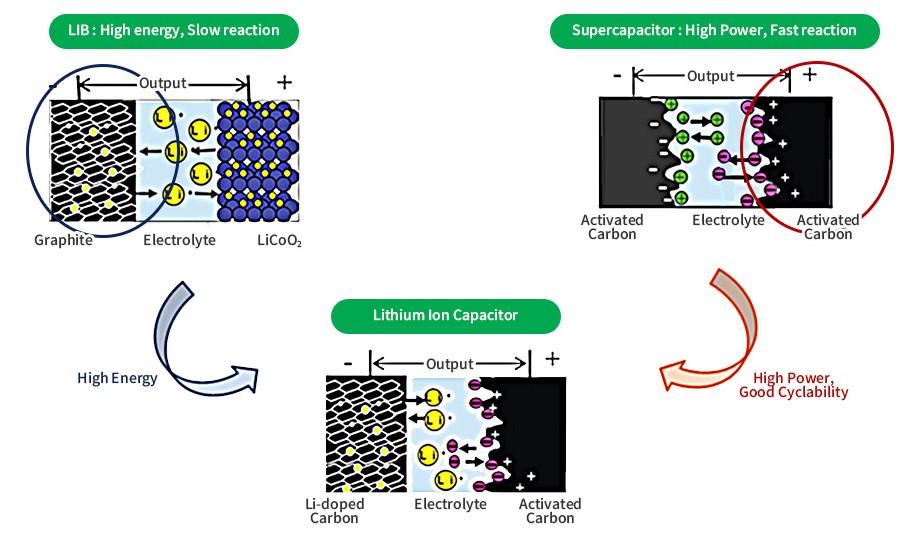
During this process, the powder also takes on a porous structure, which can increase its capacitance value. Then sinter the pellet at about 1200 to 1800℃ to eliminate impurities. Pure tantalum powder and wires are used to make the anode part.īy compressing tantalum powder around a tantalum wire, we get a “pellet” form of tantalum. Just like other capacitors, a tantalum capacitor has 3 components: an anode, a cathode, and some electrolyte. Let’s first talk about tantalum capacitors.įigure 1: Tantalum’s product shipment in 2016 In 2021, about 70% demand for tantalum is from the electronics industry: anodes for capacitors, semiconductor targets, and sintering liners for anodes.

Most tantalum is used in capacitors as anodes that belong to electronics, and others are mainly used in alloys, chemicals, and sputtering targets. Figure 1 shows tantalum’s product shipment in 2016. Due to its good physical and chemical properties, Tantalum is mainly used in the field of electronics, alloys, and other areas. It has excellent immunity to aggressive aqua regia under 150℃.

Tantalum (Ta) is a rare, hard, blue-gray, and lustrous transition metal that is highly corrosion-resistant and conductive to heat and electricity.
